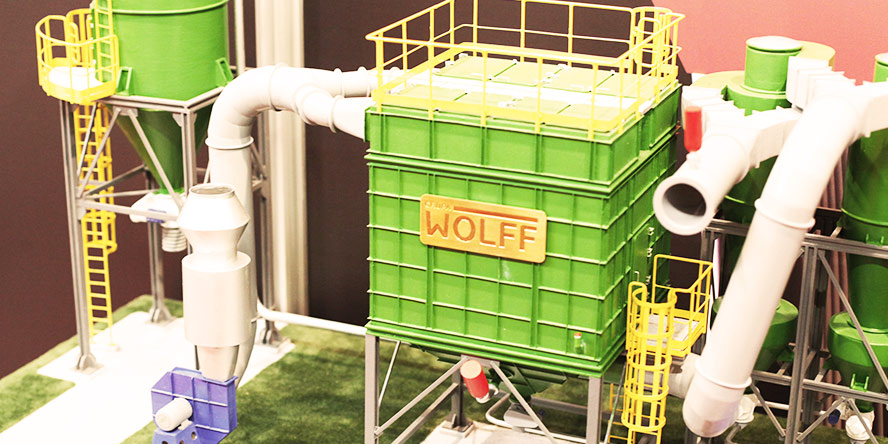
Słyszy się, że modelarstwo to jedynie zabawa dla dużych chłopców. Czasem jednak swoją pasję można wykorzystać w pracy. Janusz Warmus, nasz projektant technolog, opowiada o tym, w jaki sposób czerpał ze swoich umiejętności modelarskich przy tworzeniu makiety odwzorowującej przemysłową instalację odpylania. Wywiad został opublikowany w czasopiśmie Express Przemysłowy.
Redakcja: Jest Pan amatorem czy może przygoda z modelarstwem zaczęła się już wcześniej?
Janusz Warmus: Z tym amatorem to nie tak na 100%. Przez kilka wcześniejszych lat wykonywałem modele okrętów, ale były to zawsze zestawy, w których większość podzespołów, konstrukcja oraz instrukcja montażu były już w pewnej części gotowe.
R: Mówi się, że modelarstwo to jedynie zabawa dla dużych chłopców. Jak odniósłby się Pan do tego stwierdzenia?
JW: Myślę, że po części tak jest. Takie zajęcie daje sporo frajdy, ale w tym przypadku to była również praca, a połączenie pracy i zabawy to najlepsze rozwiązanie.
R: Jak rozumiem, propozycja stworzenia modelu instalacji odpylającej nie była przypadkowa?
JW: Od przeszło czterech lat pracuję na stanowisku projektanta technologa w GRUPIE WOLFF, która realizuje szereg projektów w branży przemysłowej. Wśród wielu działań biura projektowego jest np. wykonawstwo instalacji odciągowo-odpylających m.in. dla przemysłu energetycznego, spożywczego, drzewnego, chemicznego, a także w metalurgii i odlewnictwie. Ponieważ szczególny nacisk kładziemy na realizację inwestycji, które związane są z odpylaniem palnych i wybuchowych pyłów, gazów, par cieczy oraz mieszanin hybrydowych, do istniejących lub projektowanych instalacji opracowujemy koncepcję zabezpieczeń ograniczających ryzyko i skutki wybuchu, dostarczamy je do zakładów, montujemy, uruchamiamy, a później serwisujemy.
W 2014 roku pojawił się pomysł, by GRUPA WOLFF pojechała do Niemiec i zaprezentowała się na Targach Schuttgut w Dortmundzie. Mieliśmy tam pokazać stworzoną przez nas koncepcję Dedykowanego Systemu Bezpieczeństwa Wybuchowego, ale zależało nam na tym, by zrobić to na praktycznym i jednocześnie przykuwającym wzrok przykładzie. I wtedy zrodziła się idea stworzenia makiety instalacji odpylającej, która de facto wywarła na zwiedzających szczególne wrażenie.
R: Co, oprócz pomysłu, było podstawą do realizacji tego zamierzenia?
JW: Gdy zaszła konieczność wykonania modelu instalacji odpylającej, jedną z ważnych decyzji było dobranie odpowiedniej metody pracy. Wybór padł na metodę tradycyjną, opierającą się głównie na standardowych materiałach modelarskich, czyli sklejce, mosiądzu, niewielkiej ilości tworzyw sztucznych, różnego rodzaju klejów oraz szpachli. Podchodząc do zadania, trzeba było sięgnąć do podstaw sztuki modelarskiej i rozpocząć od wykonania wstępnych założeń na temat tego, jak instalacja ma wyglądać.
R: Jaka była więc koncepcja projektu?
JW: Przede wszystkim należało wybrać urządzenia, które GRUPA WOLFF posiada w swojej ofercie, czyli klasyczny filtr workowy oraz cyklony (urządzenia często stosowane w energetyce). Dodatkowo urządzenia te należało wyposażyć w odpowiednie systemy przeciwwybuchowe, tak jak ma to miejsce na prawdziwych instalacjach.
Kolejnym krokiem było przygotowanie dokumentacji, która pozwoliła na łatwe wykonywanie modeli – w tym wypadku były to wydrukowane w odpowiedniej skali rysunki, co pozwoliło na szybkie i łatwe zbieranie wymiarów bez konieczności ich ciągłego przeliczania.
R: Wybrali Państwo urządzenia, wykonali dokumentację i co dalej?
JW: Gdy powyższe założenia były gotowe, przyszła kolej na zbieranie materiałów, które mogliśmy wykorzystać do pracy nad projektem. Na szczęście wybór odpowiednich tworzyw nie sprawił wiele kłopotów, gdyż w dzisiejszych czasach Internet jest skarbnicą bez dna – praktycznie każdy niezbędny element da się kupić w sklepach modelarskich. Trafiliśmy na szeroki asortyment materiałów, które są konieczne do zbudowania odpowiednich części modelu.
Przykładowo były to różnego rodzaju sklejki, które stały się podstawą obudowy filtra, deseczki i listewki, stanowiące konstrukcje podporowe, stężenia czy szkielety urządzeń. Wskazać również należy pręty i płaskowniki oraz siatki z mosiądzu, które pozwoliły na wykonanie drabin, podestów, krat pomostowych i barierek.
R: Materiały zostały zakupione, więc przyszła pora na działanie…
JW: Po zakupieniu pierwszej partii materiału rozpoczęła się budowa urządzeń. Na pierwszy rzut poszła konstrukcja i obudowa filtra workowego, jaki w rzeczywistości został przez GRUPĘ WOLFF wykonany i dostarczony do jednej z elektrowni. Był to filtr o konstrukcji wzmocnionej, w wykonaniu przeciwwybuchowym i z odpowiednimi zabezpieczeniami, przeznaczony do współpracy z instalacją odpylającą pyły tworzące mieszaniny wybuchowe.
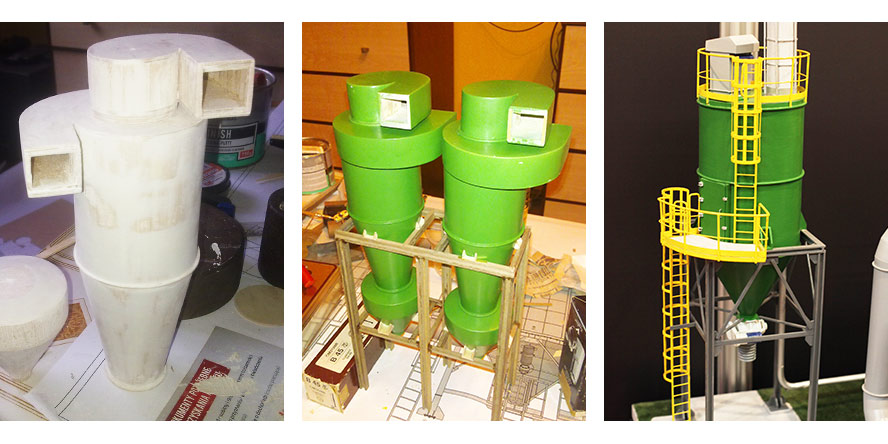
R: Jak przebiegały prace nad modelem filtra? Czy pojawiały się jakieś trudności?
JW: Sama obudowa nie stwarzała dużo problemu, gdyż jej podstawą była konstrukcja zbliżona do sześcianu, do której zostały doklejone odpowiednio przycięte sklejki. Kolejnym krokiem było wykonanie leja zsypowego, który również nie wymagał dużego nakładu prac. W rzeczywistości były to sklejone trójkąty o odpowiednich wymiarach.
Kiedy obudowa została wykonana, należało dodać naszemu modelowi charakteru. Z wykonaniem żebrowania konstrukcji ścian odpylacza wiązały się jednak czynności, które wymagały dużo większej cierpliwości i nakładu prac. Był to moment, w którym znowu trzeba było wrócić do zakupu kolejnych materiałów. Listewki mające symulować płaskownik o grubości 8 mm i o przykładowej szerokości 50 mm musiały być odpowiednio małe. Na szczęście i w tym przypadku pomogła bogata lista sklepów internetowych, ale zanim znalazłem odpowiedni materiał, musiałem odwiedzić kilka z nich.
Aby przygotować wspomniane żebrowania konstrukcji ścian odpylacza, na jego obudowie naniosłem ołówkiem linie, po których miały biec żebra. Może się to wydawać bardzo proste, jednak aby zrobić je precyzyjnie, poświęciłem na to sporo czasu. Następnie, po docięciu listewek, zacząłem je stopniowo doklejać do konstrukcji. Okazało się, że będzie to mozolna praca, gdyż dostępne na rynku kleje do drewna na tyle wolno wiązały, że część listewek się pochylała/odchylała/odstawała. W związku z tym zaszła konieczność dodawania pomocniczych elementów stabilizujących, które zostały wyjęte po całkowitym związaniu kleju. Aby zająć się kolejną ścianą, trzeba było odczekać kilka godzin, aż klej zwiąże, gdyż delikatne uderzenie mogło spowodować zniszczenie już wykonanej pracy.
R: Stworzenie jednego urządzenia wiązało się z mozolną pracą… Co było kolejnym etapem?
JW: W kolejnym stadium prac przyszła pora na konstrukcję podporową filtra. W tym celu zastosowano listewki z drewna orzechowego. Dobrze trzymający i stosunkowo twardy materiał pozwalał na wykonanie belek kształtem zbliżonym do profilu HEB, należało jedynie skleić listewki na jeden profil. Wtedy okazało się, że źle przekalkulowałem niezbędną ilość materiałów. Po ich uzupełnieniu prace mogły być kontynuowane.
R: Prawie gotowy filtr nie wyglądał jeszcze tak, jak powinien – ściany przecież nadal były drewniane.
JW: To prawda. Kolejne prace związane były z malowaniem filtra. To wydawało się proste – farba podkładowa w aerozolu, następnie nawierzchniowa i gotowe. I tutaj się pomyliłem.
Podkład nie krył powierzchni właściwie – wszelkiego rodzaju zakamarki nie zostały dokładnie pokryte farbą. Trzeba było zatem zmienić system malowania. Postawiłem na mocno rozcieńczoną farbę i pędzel. W takich sytuacjach należy pamiętać o tym, by nie zmienić typu/rodzaju farby. Popełniłem jednak błąd i farba się zważyła (jeśli nałoży się warstwę farby o innym składzie na już gotową, to może dojść do sytuacji, w której nastąpi reakcja chemiczna powodująca jej degradację, przykładowo pofałdowanie). Potrzebna więc była szybka reakcja – należało usunąć całą farbę niewielkim śrubokrętem i rozpocząć malowanie od nowa. Po nauczce z popełnionych błędów dalsze prace odbywały się bez zarzutu.

R: Jakie urządzenia oprócz filtrów obejmowała makieta?
JW: W kolejnym etapie zająłem się tworzeniem cyklonów z konstrukcją wsporczą, czyli klasycznych urządzeń, które w rzeczywistości służą do mechanicznej separacji pyłu z gazów przemysłowych. W cyklonach do oddzielania cząstek stałych wykorzystuje się siłę odśrodkową działającą na cząsteczki pyłu.
Podczas prac przypomniały mi się czasy wykonywania deskowania poszycia burt okrętów. Należało zrobić szkielet obejmujący ślimak wlotowy i lej cyklonu, do których stopniowo doklejało się lipowe listewki o odpowiedniej długości. Do wyrównania linii deseczek na sam cyklon zużyłem mnóstwo szpachli. Klejenie listewek lipowych za pomocą wodorozcieńczalnego kleju nie było proste, gdyż schnie on stosunkowo wolno, powodując rozmiękanie całej konstrukcji. Podobnie jak w przypadku żebrowania konstrukcji ścian filtra trzeba było spowolnić prace i dodawać elementy wzmacniające. Potem przyszedł czas na konstrukcję wsporczą i malowanie – to już zostało wcześniej przetestowane, więc poszło jak z płatka.
R: Umówmy się, że filtr i cyklony to większe konstrukcje na makiecie. Ale przecież oprócz nich widzimy inne drobne elementy konstrukcyjne, takie jak np. drabiny czy barierki.
JW: Oczywiście, wykończenie naszych urządzeń wymagało sporej precyzji. Kiedy przyszła kolej na podesty i drabiny, aby jak najlepiej oddać ten typ konstrukcji, na materiał wybrałem mosiądz. Zdecydowałem również, że poszczególne elementy będę łączył poprzez lutowanie. Założenia wydawały się proste, jednak lut miękki na mosiądzu dla tak cienkich materiałów nie należał do najłatwiejszych. Po pierwsze, każdy lut wymagał wytrawienia miejsc styku i pobielenia przed łączeniem (po wytrawieniu metalu pokrywa się go cienką warstwą lutu cynowego, która będzie umożliwiała dalsze łączenie lutowanych elementów). Dodatkowo okazało się, że każdy kolejny lut powodował roztapianie już gotowego, więc trzeba było pracować szybko i na tyle dokładnie, żeby nie musieć robić poprawek.
R: Jakie dodatkowe urządzenia oprócz filtra i cyklonów obejmowała instalacja?
JW: Były to wentylator z akcesoriami, tłumik, silos oraz podstawa, na której wszystko zostało zmontowane.
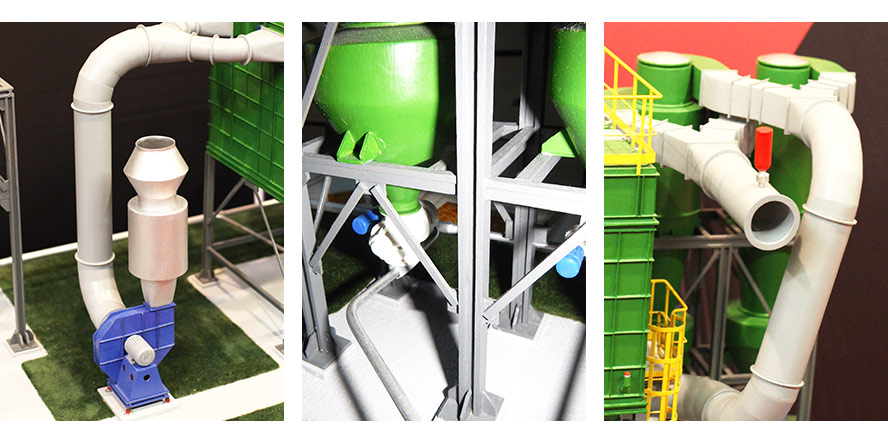
R: Wspominał Pan na początku o zabezpieczeniach przeciwwybuchowych, które stanowią dopełnienie całej instalacji – jakie rodzaje zastosował Pan na urządzeniach znajdujących się na makiecie?
JW: Oczywiście, „wisienką na torcie” były systemy przeciwwybuchowe. Na górze cyklonów umieściłem panele dekompresyjne. W rzeczywistości służą one do odciążania wybuchu, czyli wyprowadzeniu jego skutków, tj. płomienia, ciśnienia, spalonego i niespalonego produktu oraz gazów spalinowych, poza chronione urządzenie. Panele dekompresyjne są ekonomiczną alternatywą dla innych zabezpieczeń przeciwwybuchowych, jednak należy zachować dużą ostrożność przy ich doborze. Niepoprawnie zastosowane stanowią poważne zagrożenia zarówno dla instalacji procesowej, jak i dla personelu.
Początkowo nie mieliśmy pomysłu, z czego wykonać taki panel. Jeden z kolegów, z którym pracowałem przy projekcie, wpadł na pomysł, by zastosować denko po puszcze od coca-coli. Okazało się to świetnym rozwiązaniem.
Jeśli chodzi o filtr, „zainstalowałem” na nim czerwone butle HRD, będące jednym z elementów systemu tłumienia wybuchu (w rzeczywistości system posiada jeszcze czujniki ciśnieniowe i/lub optyczne), którego działanie polega na wykryciu zarzewia wybuchu w jego bardzo wczesnej fazie. Zaraz po tym zostają aktywowane butle HRD, które wprowadzają do wnętrza chronionego aparatu specjalny proszek tłumiący. Dzięki temu wybuch zostaje stłumiony, zanim jego ciśnienie osiągnie niebezpieczny poziom.
Aby model był w zakresie bezpieczeństwa wybuchowego kompletny, niezbędne było również dodanie podzespołów, które stanowią odsprzęganie wybuchu, czyli uniemożliwiają cofnięcie się fali wybuchu przez instalacje na stanowiska pracy bądź do urządzeń technologicznych. Tutaj zastosowałem butle HRD, których modele umieszczone zostały na rurociągach (odpylającym oraz rurociągu transportu pneumatycznego), a także dozowniki celkowe zlokalizowane pod lejami zsypowymi filtrów oraz silosu.
R: Ile czasu zajęło uzyskanie efektu finalnego całej makiety?
JW: Trudno mi odpowiedzieć na to pytanie, ponieważ od wykonania makiety minęło już kilka lat, co oczywiście nie oznacza, że makieta nadal nie „pracuje”. Wydaje mi się, że było to około 2–3 miesięcy. W tym okresie praktycznie każde popołudnie po pracy i całe weekendy spędzałem nad modelami. Mimo że poświęciłem na to sporo czasu, były to naprawdę fajne miesiące.
R: Czy jest Pan zadowolony z efektu finalnego? Jak ocenia Pan cały projekt?
JW: Ten projekt był naprawdę ciekawym wyzwaniem. Na co dzień mam styczność z takimi instalacjami, zarówno pod kątem projektowym, jak i wykonawczym, więc stworzenie makiety w mniejszej skali było z jednej strony łatwe, gdyż sam opracowałem koncepcję tego, jak będzie ona wyglądała, i mogłem w miarę szybko reagować na problemy.
Z drugiej jednak strony musiałem pamiętać, że szef obdarzył mnie stuprocentowym zaufaniem, przecież miał właściwie zobaczyć wszystko na samym końcu, więc musiało to dobrze wyglądać. W każdym razie efekt był zadowalający, choć z dzisiejszej perspektywy niektóre elementy zrobiłbym lepiej. Przykładowo w realizowanym projekcie zapomniałem wykonać skrzynki przyłączeniowej do silnika, ponadto przydałaby się również instalacja elektryczna czy modele szafek sterujących.
Chciałbym również podkreślić, że bez Kolegów i Rodziny, którzy mi pomagali – Marcin Sobczyk, projektant z GRUPY WOLFF, i inni pracownicy firmy oraz znajomi, którzy udzielali nie tylko porad, pomocy własnych rąk, ale również i sprzętu, którym nie dysponowałem – projekt nie zakończyłby się sukcesem.